VAM Software was developed by Fleming & Associates Calibration, Inc to replace the existing VAM data panel with a PC front-end. This single menu driven application allows for all programmable part configurations and data acquisition. The PLC (GE Series 90-30 programmable controller) will continue to control the VAM hardware and is directly interfaced with the PC using the SNP protocol over an RS-232C connection. An Analog to Digital (A/D) interface board is resident in the PC and is utilized to monitor various VAM outputs (just as the PLC). In addition, an RS-232C connection is established with the Micro Infrared Temperature Transducer which allows the PC to set preprogrammed emissivity values for each part number.
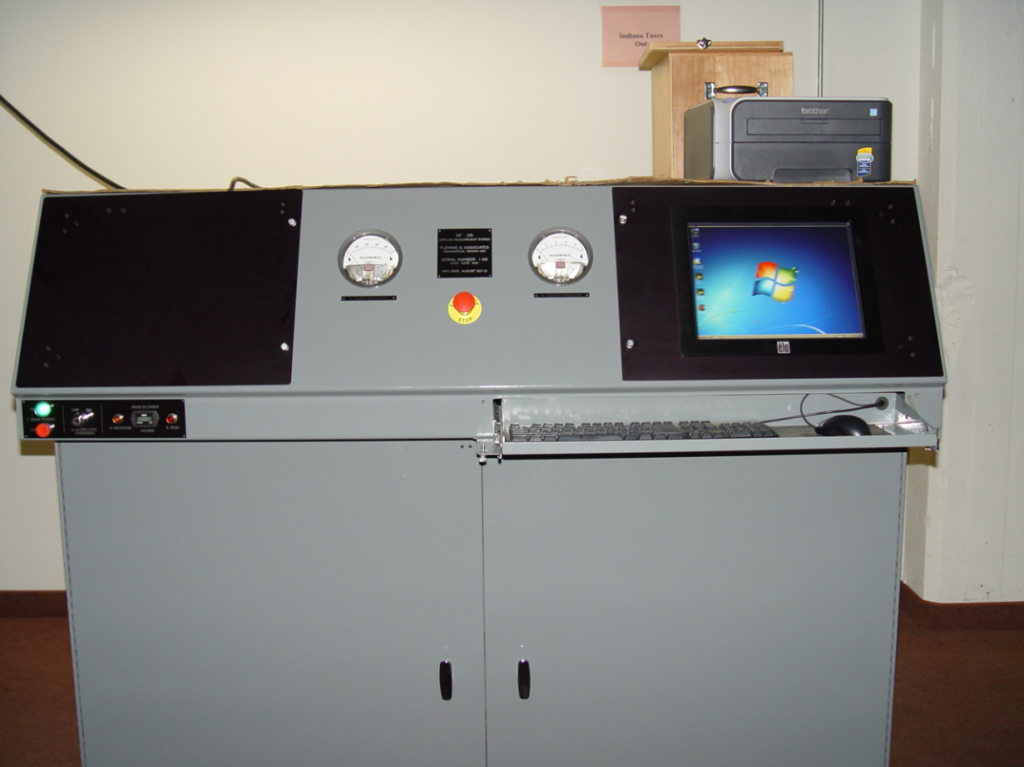

FILE SERVER
|
AF16-S & AF-36 Flow Files |
AF16-S Data Files |
AF36 Data Files |
VAM Data Files |
Adjustment Data Base |
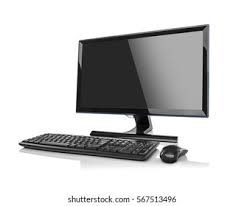
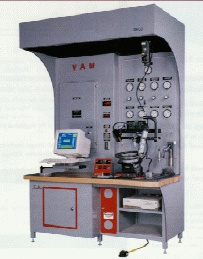
With the addition of a PC to the VAM, there is, considerable improvements in data acquisition, enhanced process controls, and the operator interface. In this, vane adjustment data is automatically captured and can be used to develop correlations between vane adjustments and airflow measurements, as well as, Statistical Process Control purposes. It is now possible to improve control over the adjustment process by allowing operators to specify “part set-ups” (by part number) and configure specific VAM settings to ensure adjustments are performed consistently. A more “user friendly” environment is established by means of providing help screens and a comprehensive user interface. Use of MS/PCDOS and PCs provides a standardized platform familiar to engineers and operators.
VAM Software is similarity to Fleming Software:
- VAM Screens and AF36 Screens
- VAM System Configuration and AF36 System Configuration
- VAM “Part Record” and AF36 “Part Record”
VAM operation screen is graphical similar to the AF16-S Operation Screen
VAM Software computer linking with Fleming & Associates
Airflow Measurement Systems:
- Support staff can monitor, analyze and maintain data without interrupting production
- Consistent Data Entry
- Data backups. By storing data on a file server only one hard drive must be backed up
- Automatic updates.
The VAM software can read pre-adjustment Airflow values directly from AF-36 or AF16 data files. Also, the Airflow Systems can write post adjustment Airflow information directly the adjustment database when parts are measured after the adjustment. This improves data integrity.
VAM COMPUTERIZATION (PC Based Model)
Due to Industry request, now offers a PC based version of the VAM for Operators who need expanded parameter control and enhanced data collection capabilities. The PC model has the same basic functions as the Operator Interface model plus many advanced features. The PC model still retains the original Programmable Logic Controller (PLC) but has several new features such as:
- Programmable and record able hydraulic pressures for Clamp and Bend pressure
- Programmable infrared temperature emissivity parameters to accommodate different vane ring materials
- Visual “real time” indication and storage of trailing edge trace data (by vane number)
- Height of Bend versus airflow correlation capability
- Recommended Torch Time and Bend Hold Time, for each vane ring part number
- Safety software to deny machine capability to enable Bend Mode if an excessive amount of time has elapsed between temperature measurement and Bend Mode.
- Simplified setup routines for Torch, Infrared Temperature, and Bend positions
- Password protection for certain buyer specified parameters
- Software limits to prevent table advancement (prior to bending) if vane temperature is not in within the specified tolerance limits
- Average Bend Height adjustments for entire vane ring
- Preheat cycle/ for each vane ring for a maximum of 99 seconds per Preheat cycle
- Visual indication of “real time” hydraulic pressure and linear displacement of bend head.
- Auto routine for “cold bending”.
- Programmable Max Allowable Bend parameter.
- Automatic clockwise/counterclockwise rotary table rotation selection (by vane ring part number).
- Parameter tables to allow listing of variable process parameters by vane ring part number.
- Data storage, retrieval, and display of items such as:
- Engine serial number.
- Engine model number.
- Pre-adjustment EFA/Class.
- Target EFA/Class.
- Post adjustment EFA/Class.
- Deviation of conformance to correlation.
- Height of Bend.
- “Pre” and Post Trace data for vane height with respect to no. “one” vane.
- Vane ring part/serial numbers.
- Work order number.
- Rework code.
- Time (including cycle time).
- Bend and chuck Jaw part numbers for each associated vane ring part number.
- Number of airfoils in vane ring.
- Capability for recommended “Height of Bend” vs. Effective Flow Area (EFA) correlation routines. (Buyer to do actual data collection & entry of same).
- Flame dwell time.
- Actual hydraulic pressure used for Clamp & Bend cycles.
- Printability of selected software parameters.
- Programmable Trace, Jog, and Run rotary table velocities.
- Airfoil temperatures (maximum and last temperature sample prior to bending a particular vane airfoil).
- Emissivity for infrared temperature correlation (by vane ring part number).
- Manual 7 Auto mode routines.
- Preheat time and number of cycles.
- Capability (with some hardware/software modifications) for computer networking with airflow rigs such as Fleming (or equivalent) type flow rigs and / or other computer systems.
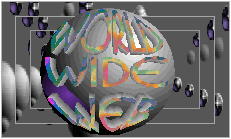