VANE ADJUSTMENT MACHINE (VAM) – is the World Class Vane Adjustment for Turbine Engines
SIFCO VANE ADJUSTMENT MACHINE (VAM) – was designed, developed, and built by SIFCO Turbine Component Services (Minneapolis, MN.) with cooperative efforts in automation and software design and development by INTERLOCK SYSTEMS Inc. (Minneapolis, MN.). Software for the PC model was designed and developed by Fleming & Associates, Inc. (Indianapolis, Indiana).
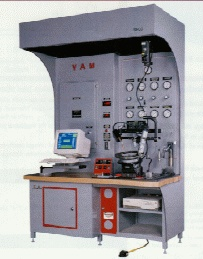
Why VANE Adjustment?
- To achieve Proper Vane Area/s or Class as Specified by OEM for:
- Casting Vendors (Double Dimensioning?)
- Repair& O/H Facilities
- Test Cell Facilities.
- To Match or Correlate with other components in the Engine for Purpose of Achieving Proper Engine Parameters such as:
- Exhaust Gas Temperature (EGT)
- Speed Matching Between Turbine Sections
- Power Levels
- Fuel Efficiency.
VAM is the first “commercially available” automated machine of its type to solve the types of problems, which have plagued the Jet Engine Industry for many years.
Some of the possible benefits associated with the VAM are as follows:
- Reduction of Skill Level required to adjust Vane Rings;
- Reduction of Vane Ring Adjustment time;
- Achievement of Correct Airflow after only One Adjustment;
- More Accurate Vane Adjustment with Resultant Product Improvement;
- Reduction of Spare Vane Ring Inventories since VAM can quickly adjust Vane Rings to Airflow required by multiple part numbers;
- More Uniform Bend Contours from Vane to Vane (Aerodynamically improved).
- Less Vane Ring Cracking and Resultant Scrap/Rework;
- Quicker Processing time during Vane Ring Overhaul;
- Vane Throat (Exit Area) Equalization more easily achieved;
- Possible Improved Engine Performance and Efficiency;
- Casting Vendors can Now Produce Vane Ring Castings which are both Dimensionally Correct and within desired Airflow Specifications with Reduced Time and cost;
- Vane Ring can be Easily adjusted in both the “Casting” and “Assembly” Configurations;
- Jet Engine Test and overhaul facilities would not have to send Vane Rings outside the company for Delicate Vane Adjustment. This could also minimize Delays in Test Cell Runs, if engines require Vane Adjustment for Flow Area Correlation;
- Matching of Airflow Characteristics of Compressor and Power Turbine Vane Rings could Yield a higher “First Time” Success Rate during Test Cell Runs;
- The VAM could be integrated at a later date (with additional hardware and software) with presently available Airflow Equipment to form a Work Cell Capable of Computerized Data Collection, Statistical Process Control, and development/Collection of “Real Time” and Historical Bend Data for Process Improvement;
- Due to simplicity of use, the VAM would enable enhanced flexibility of the Work Force since it is relatively easy to use and does not require a dedicated Craftsman to perform Vane Adjustment.
The overall operation of this machine takes a highly skilled “Black Art” type operation, and transforms it into a fast, predictable, and accurate process which can be learned in one day (or less) by any Operator regardless of skill level, and greatly reduces scrap and rework of extremely expensive jet engine vane rings.
The exit area of the turbine nozzle vane ring is the most critical part of the turbine design. If the vane area is too large, the turbine will not operate at its best efficiency. If the area is too small, the nozzle will have a tendency to choke and loose efficiency under maximum thrust operating conditions. Other specific maladies can manifest themselves in the form of improper engine speed matching, extreme engine temperatures, and excessive fuel consumption. Vane area is defined as the total cross-sectional area of the exhaust gas passages at their narrowest point, which is usually at the trailing edge. The collective areas of each vane area, is usually measured by flow type measurement, using an Airflow rig.
Adjustment of vane ring areas – is the main purposes for using the SIFCO Vane Adjustment Machine (VAM)