Fleming & Associates Calibration, Inc. is a pioneer in the aerospace industry with a focus on Airflow Measurement Equipment, Calibration, Software Engineering and Adaptor designand production. Since its creation in 1974, we have become a world leader in the production of airflow measurement systems. Fleming equipment is successfully used to determine the aerodynamic area of various components such as gas turbine nozzles, nozzle segments, wheels, combustion liners and other similar components, parts and units for aircraft and helicopter engines, and land-based power generators. To date, approximately 80% of all small turbine engines throughout the world have components measured on Fleming designed Airflow Measurement Systems. With Fleming Equipment and Calibration Services, turbine engines can be tested more accurately, more efficiently, and quicker than even before. This allows for better quality and safer engines to be released for their various uses. We provide timely and reasonably priced quality airflow measurement systems, adaptors, calibration service, products support and training.
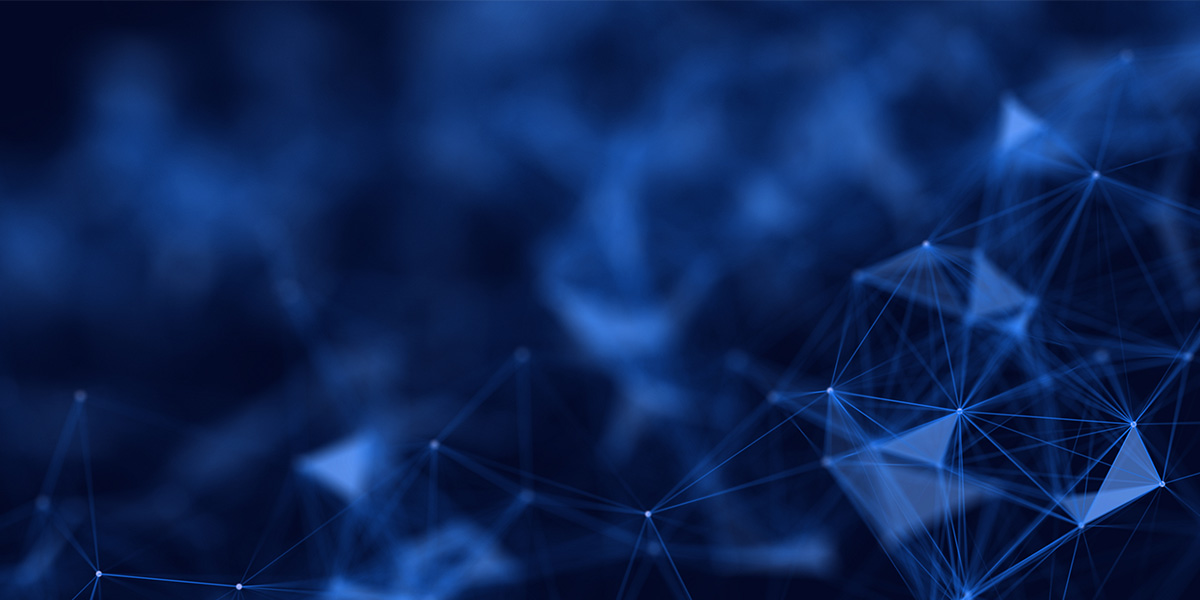
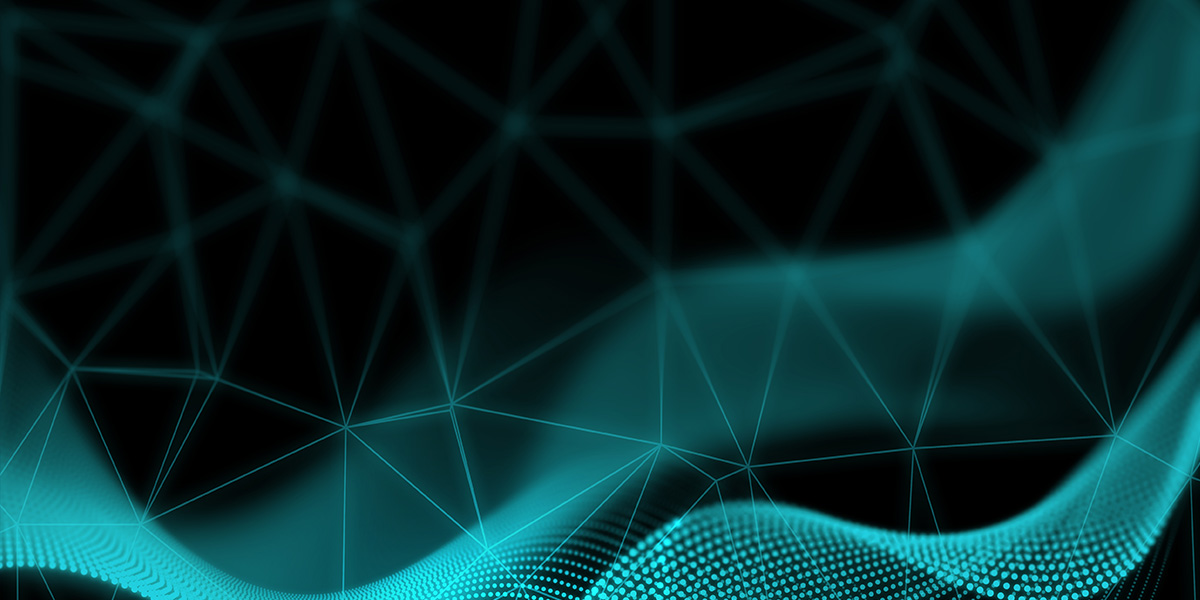
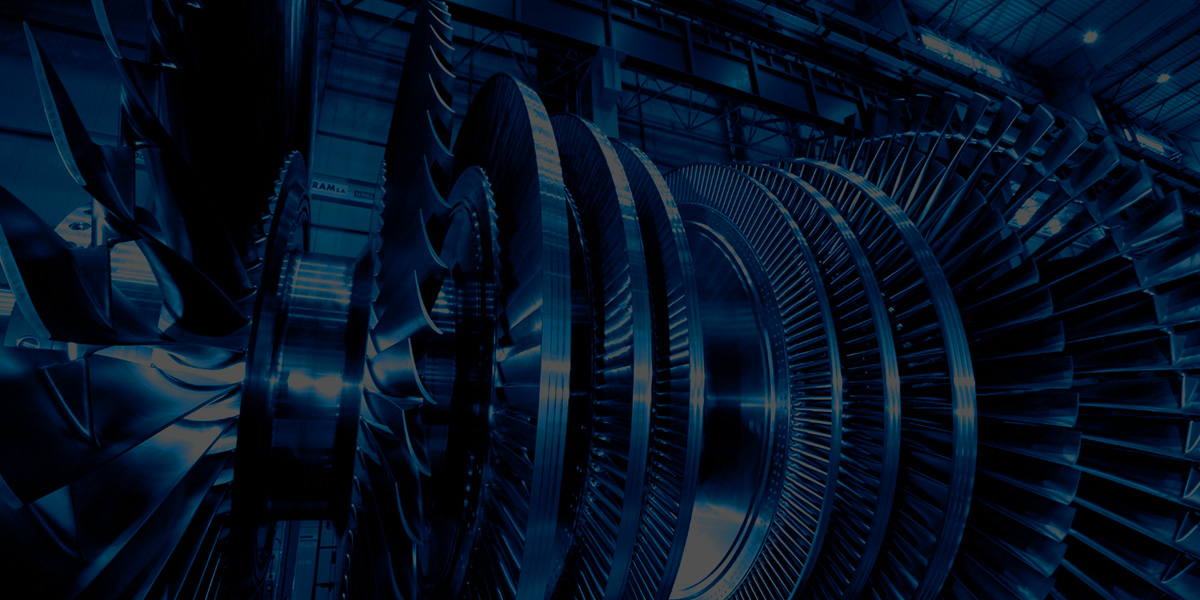
The flagship product of Fleming & Associates Calibration, Inc. - the Airflow Measurement System is the industry standard in dynamic airflow measurement for such critical components as gas turbine nozzles, nozzle segments, wheels, combustion liners and other similar components. Fleming & Associates Calibration, Inc. provides Airflow Measurement Systems for various branches of Industry such as Aerospace, Trains and Ships, Generators, Automotive, and Land based power generation.
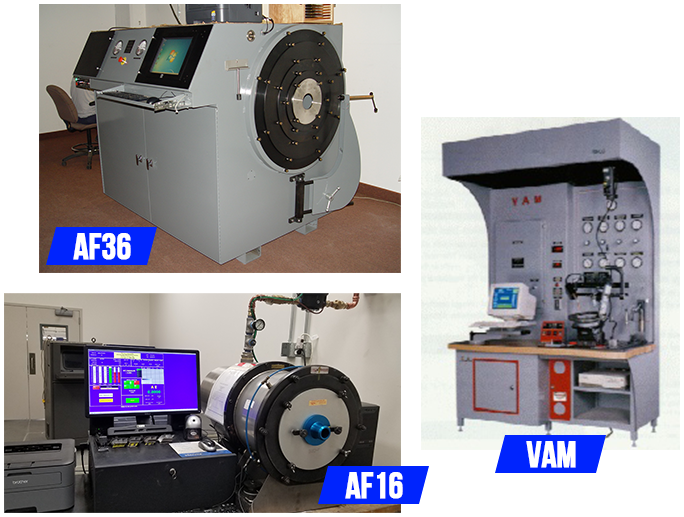
Fleming & Associates Calibration Inc. has been providing Airflow Adaptors for more than a generation and leading the industry in Adaptors design and manufacture. The accuracy of measurement is strongly is strongly influenced by Adaptor design and manufacture we listen to what our Customers want and help them decide what they need. Over 250 various types of segment and annular Adaptors for a wide range of gas turbine components designed using our experience and tested to ensure Customer satisfaction.
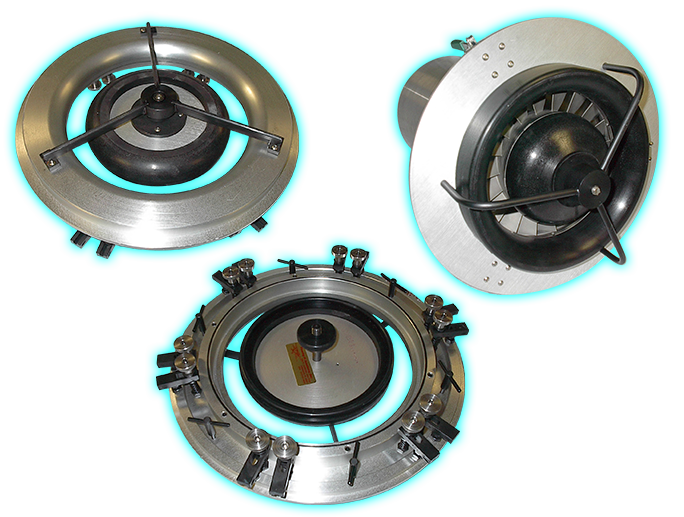
You can TRUST.
SERVICE is our #1 priority. We are keenly aware that when implemented, our Measurement Equipment becomes absolutely essential to the production process.
Fleming & Associates Calibration provide onsite technical Service for Inspection and yearly Calibration of delivered Airflow Measurement Systems to insure that the Equipment is functioning properly and within the required accuracy and repeatability ranges. Our Company objective: to serve and support the Aerospace Industry with the most reliable and efficient Airflow Measurement Systems and Adaptors available today. We carry a complete inventory of replacement parts in stock. Our staff is available to provide excellent Customer Service and Product Support.

Fleming Airflow Measurement Equipment is created based on the benefits of aerodynamic methods of measuring and provide efficient reliable, repeatable and accurate test results. Measurement data is stored on disk in a fully documented format. Airflow measurement will improve your manufacturing and/or overhaul process:
Fleming & Associates will quote any airflow measurement job you have – Aircraft, Automotive, or Land based power Generation.
Fleming Airflow Measurement Systems:
AF36 – is the only industry standard being utilized for part-area measurements ranging from 0.265 to over 150 square inches;
AF16–S – is a great, low-cost alternative for high production facilities and is intended for parts under 10 square inches, uses a sonic nozzle to control mass flow.
Fleming Airflow Measurement Systems are designed to be controlled by IBM PC compatible computers. The use of PCs provides a standardized platform familiar to engineers and operators. The user-friendlymenu-driven approach makes airflow measurement an easy task to perform. Built in Quality Control Checks provide confidence. Off-line definition of measurement parameters allows consistent methodology.
The primary advantage of airflow testing over mechanical gauging is that airflow testing requires only a small fraction of the time required to gauge a component mechanically, and avoids the expense of calibration and repair of gauges. The area is measured dynamically through transfer standards, air pressures, temperatures, and blower speeds. This is accomplished by the system adjusting blower speed to obtain the desired differential pressure across the component being measured, and then calculating the area as a function of blower speed and the other above measurements.
Fleming Airflow Measurement Equipment is successfully operated in over 100 facilities worldwide.
We have a Customary base that includes most every entry in the gas turbine engine field.
CUSTOMERS & PARTNERS
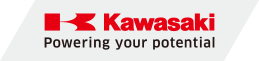
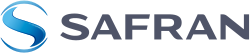

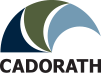
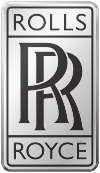
